- 27 Sep, 2017
- Solar Training , Products , Using and installation
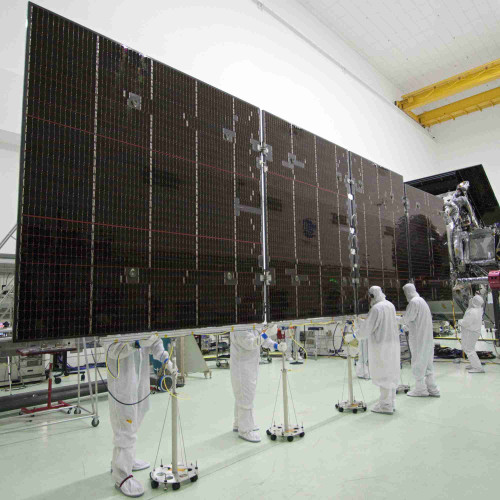
Manufacturing solar panels follows a certain procedure. First, solar-grade silicon must be produced. It is then transformed into silicon plates. Solar cells are based on silicon plates. The cells are then assembled into solar modules, which are fitted to a mounting system together with the electronic and electric components. Let's look at the first step: how silicon, the raw material in 90% of the solar panels available on the market, is processed further. Let the chemistry lesson begin!
PRODUCTION
Silicon is derived from Silica, which is found abundantly in nature, in quartz or in sand. The most common method is to extract silicon from quartz to create metallurgical silicon which will then be purified to give solar-grade silicon. The latter is then poured into ingots from which are drawn the silicon plates with which the cells are made.
SILICON REFINING
From Silica to Metallurgical Silicon
Silicon is therefore obtained from the Silica (SiO2) contained in quartz by carbothermic reduction in an arc furnace.
It is actually a matter of extracting oxygen from Silica (SiO2) by heating quartz with carbon-containing species such as coal for example. These carbon species under the effect of heat will combine with quartz oxygen to form carbon monoxide (CO) and then carbon dioxide (CO2). The heat required for the reaction is provided by the electric arcs created by electrodes contained in the famous furnace. At the end of this process, Metallurgical Silicon (MG Si) is obtained which is not yet usable for the creation of solar panels.
Purification of Metallurgical Silicon
Metallurgical Silicon must be purified in order to obtain a solar grade Silicon that can be used to manufacture solar cells. This purification can be done in different ways but the chemical technique is the most widely used.
Chlorine is used in principle because of the strong attraction of silicon atoms and chloride ions (Cl-). These compounds are then purified by distillation and thermal decomposition.
CRYSTALLIZATION AND PLATE FORMATION
The solar or polycrystalline silicon obtained in the previous step will then be melted and re-solidified into ingots. It is from these ingots that the silicon wafers that will be used to make the cells are finally cut. Indeed, it is when the silicon is molten that dopants are added so that an electric current is formed within the cells.
From this stage on, you differentiate between monocrystalline and polycrystalline panels.
Monocrystalline silicon consists of a single crystal; a drawing is carried out to form a cylindrical ingot from a single crystal strain (Czochralski process).
Polycrystalline silicon is a mosaic of crystals obtained by casting in an ingot mould slowly cooling everything down.