- 27 Sep, 2017
- Solar Training , Using and installation
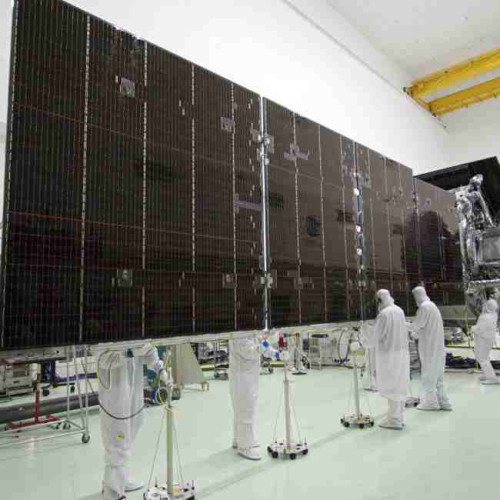
You already know how silicon plates are manufactured. Now, let's turn to the next step: how are these silicon plates processed further into solar panels? Cell manufacturing, assembly, connecting... A short overlook of all the relevant processes.
Manufacturing the solar cells
Once the silicon wafers have been formed and cut, the next step is to exploit the semiconductor properties of the material and transform the light energy into electrical energy. The photovoltaic effect, which we detailed in a previous article (link) consists of a transfer of energy from the photons of light to the electrons of silicon that allows them to move. These electrons are then attracted out of the material via a collection electrode connected to the external electrical circuit. So how is it done?
The basic principle consists in creating different layers to bring the electric current out of the plate and feed the network. We will now look at how these different layers are manufactured.
- Pickling: p-plates doped with boron during crystallization are pickling in a chemical bath to remove surface defects created during the sawing process of the plates.
- Texturing: The surface is textured in small pyramids or funnels to improve photon collection by reducing reflection. This step can also be carried out using a chemical bath.
- Doping: the doped zone n is formed by thermal diffusion of phosphorus carried out using a passage furnace heated to a temperature between 800°C and 900°C. Under the effect of heat, a residual layer of phosphorus silicate is formed, which is then removed by chemical bath.
- Removing the plate edges: the n+ layer is then removed from the plate edges to separate the transmitter and the back side.
- Anti-reflective layer: an anti-reflective layer is applied to the front panel which also improves the conductivity of the cells by limiting recombinations between charges (i.e. reactions between electrons inside the silicon which are therefore not used to create an electric current)
- Doping of the rear panel field (p+): it is doped by diffusion of aluminium. This side also serves as an ohmic conductor with the rear electrode.
- Metallization: the electrical contacts are removed. On the front side it is a silver screen printing contact that will form the electrode - and on the back side, an aluminum screen printing contact (+ electrode).
The cell is now built. A final step will be to test the cells electrically in order to know their electrical characteristics. A sorting of the cells is then carried out which will allow the optimization of their assembly.
Assembly into solar modules
Given the fragility and sophistication of photovoltaic cells, modules are primarily used to protect them from the external environment.
But they also play a role in optimizing their performance by limiting optical losses and avoiding cell overheating, which reduces their efficiency.
Stage 1: Connecting the cells, which consists of connecting them in a chain and then interconnecting them to create a matrix.
Stage 2: Encapsulation. The cells are placed between a glass layer (front side) and a Tedlar layer (back side). This process is carried out by hot rolling.
Stage 3: Supervision. It's just a matter of making a frame for the module. This step is not mandatory.
Stage 4: Connecting the junction boxes. Junction boxes are added that contain protective diodes and allow the module to be connected to the power grid.
As for the cells, a test is then carried out under calibrated artificial light to determine the exact electrical characteristics of the PV module.